|
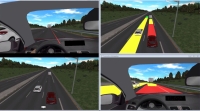
|
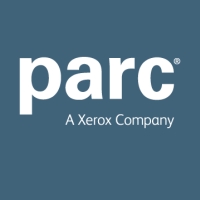 |
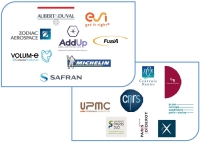
|

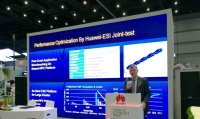
The French Minister of the Economy, Emmanuel Macron, accompanied by Muriel Pénicaud, Ambassador Delegate for International Investments, General Manager of Business France, experience the ESI IC.IDO Virtual Reality solution at the launch of the CREATIVE INDUSTRY campaign at the Hanover Fair on April 26, 2016.
|
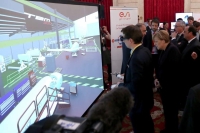
|
ESI demonstrates Daher’s use of its Virtual Reality solution ESI IC.IDO at the Elysée Palace. ©Présidence de la République/ C.Alix. |
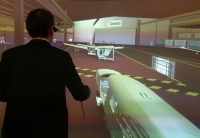 |
ESI’s Immersive Virtual Prototyping solution allows Daher’s engineers to immerse themselves inside their factory to set-up and fine-tune their aircraft final assembly lines. Image courtesy of Daher.. |
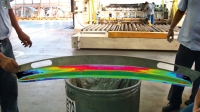 |
From simulation to reality: thanks to ESI PAM-STAMP, customer Aethra manages to compensate significant springback effects. Image Courtesy: Aethra |
|
> > Members and Partners News > ESI Group
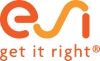
 |
Forum International de la Cybersécurité 2017
24 & 25 Janvier 2017 - Lille, France
The international Cyber Security Forum is a platform aiming at promoting a pan-european vision of Cyber Security as well as to strengthen the fight against cybercrime.
Big Data Paris 2017
6 & 7 Mars 2017, Paris, France
With over 10 500 attendees in 2016, the BIG DATA PARIS trade show is confirmed as a true not-to-be-missed event for everyone involved in the Big Data and IT sectors.
JEC World 2017
14 & 16 Mars 2017, Paris, France
Meet ESI at JEC World 2017 and learn more about ESI's Virtual Prototyping Solution for Composites Structures. You will have information on both PAM-COMPOSITES, the industrial simulation chain for the manufacturing of composites structural components and VIRTUAL PERFORMANCE SOLUTION, end-to-end simulation solution to predict the performance of composite and hybrid material parts, taking into account the manufacturing effects |
 |
January 2, 2017 -
ESI Group, leading innovator in Virtual Prototyping software and services for manufacturing industries, announces its first attendance at the Consumer Electronics Show® (CES), taking place from January 5 to 8, 2017 at the Las Vegas Convention Center. A “catalyst” supporting industry manufacturers in their digital transformation, ESI provides solutions that replace physical prototypes by virtually replicating the fabrication, assembly and testing of products in different environments. In the North Hall, on the booth 5915, ESI will present ESI Pro-SiVIC™, its solution enabling the virtual testing of the sensors serving the various perception systems onboard vehicles or aircraft, and an innovative project for a Virtual Human-In-The-Loop that addresses the cognitive aspects of product performance. Read more  |
 |
December 7, 2016 -
To Enhance System Modeling Solutions, from Faults Detection to System Reliability Analysis, and Maintainability Prediction
ESI Group, leading innovator in Virtual Prototyping software and services for manufacturing industries, announces the signing of a long-term strategic partnership with PARC, a Xerox company and renowned provider of custom R&D and technology solutions to Global 1000 companies and government agencies. The partnership initially focuses on expanding and industrializing PARC’s advanced research project on Fault Augmented Model Extension (FAME), initiated with the Defense Advanced Research Projects Agency (DARPA). The partnership encompasses system reliability modeling, system safety assessment, predictive maintenance, and condition-based maintenance. These capabilities will come to strengthen the already existing ESI solutions dedicated to helping industrial manufacturers overcome engineering issues related to complex cyber-physical systems. Read more  |
 |
November 23, 2016 -
A research program for metal additive manufacturing
SOFIA ("SOlutions pour la Fabrication Industrielle Additive métallique" - Solutions for Industrial Metal Additive Manufacturing) is an applied research program for metal additive manufacturing, initiated by the Fives Michelin Additive Solutions joint-venture.
SOFIA's ambition is to contribute to the development of this technology by working on the entire metal additive manufacturing value chain (powders, production equipment, processes). To that end, SOFIA fosters synergies between the skills provided by high-level partners. Read more  |
 |
Septembre 10, 2016 -
ESI Group, leading innovator in software and services for manufacturing industries worldwide, signed a Memorandum of Understanding (MoU) with , a leading global information and communications technology (ICT) solutions provider.
The signature ceremony took place during the event HUAWEI CONNECT 2016 in Shanghai, China on September 1, 2016. The two parties will collaborate on High-Performance Computing (HPC) and cloud computing to provide innovative industrial manufacturing solutions for customers in China and worldwide.
They also jointly released a white paper on the Huawei HPC platform-based ESI Virtual Performance Solution (VPS), a leading software solution used by industrial OEMs and their suppliers in order to test virtually all aspects of their product performance, including crash and safety. Often demanding large simulation models to achieve high levels of precision and predictive capabilities, VPS users greatly benefit from Huawei’s robust and efficient IT platforms, and the work done by Huawei and ESI to optimize the way their products work together.
Read more >>>>
|
 |
September 10, 2016 -
ESI Group, leading innovator in Virtual Prototyping software and services for manufacturing industries worldwide, announces its participation in the “Industry of the Future” program, led by the French government. ESI will provide its unique capabilities in support of the digitalization of the industry, virtualization, and the Internet of Things. Notably ESI’s Virtual Reality solution, IC.IDO, perfectly illustrates how digital technologies can be used to increase industrial competitiveness from product design to product development, product marketing, maintenance, and to optimize production.
Read more >>>>
|
 |
December 1st, 2015 -
Groundbreaking digital technology fosters industrial development and innovation
ESI Group was invited to participate in the French-German Digital Conference, held on October 27 at the Elysée Palace in Paris. During the conference, French Minister Emmanuel Macron and German Minister Sigmar Gabriel presented their “Action Plan” for an ambitious digital strategy in Europe, and related societal challenges. They were then joined by French President François Hollande, German Chancellor Angela Merkel, and President of the European Commission Jean-Claude Junker to witness demonstrations of selected innovative technologies, including ESI’s Immersive Virtual Prototyping solution as used by aircraft manufacturer Daher.
French company Daher uses ESI’s Virtual Reality solution ESI IC.IDO to optimize their assembly lines and increase productivity. Thanks to Virtual Reality, Daher’s engineers can assess assembly processes very early in the product development phase, before they commit to major investments and before any real prototype is built. The demonstration at the Elysée showed officials how Daher uses ESI’s solution to fine-tune the final assembly lines (FAL) of the TBM 900, the latest addition to the Daher’s very fast turboprop aircraft family.
Nicolas Orance, Chief Innovation Officer of Daher comments " One of the current challenges of industrial companies is the digital transformation, and Daher has been implementing a number of solutions for the Aerospace and Nuclear sectors. Virtual Reality helps us bridge the gap between design solutions and ideas, and the shop floor implementation, by gaining time and efficiency. "
During the demonstration, an ESI engineer connected from the Elysée Palace in Paris to a colleague based at ESI’s subsidiary in Stuttgart, Germany. Remotely, both engineers were immersed in the same 3D scene. They demonstrated a typical collaborative project review, working on the same virtual prototype — a best practice to enable reliable decision making, upfront in the product development process.
Vincent Chaillou, COO, ESI Group comments " With its unique Virtual Prototyping offering addressing various industrial sectors, ESI is well equipped to support European initiatives for developing digital technologies, such as Industries du Futur and Industry 4.0."
Fouad El-Khaldi, General Manager of Strategy and Innovation, ESI Group, puts it in the context of the local economic development " This event illustrates the great potential of European companies, and especially Mid-Cap companies, to drive industrial growth in Europe with the help of digital technologies. Such collaborations with industrial players, as well as governmental bodies act as an efficient catalyst to increase Europe’s innovation ecosystem and industrial competitiveness. To this aim, ESI takes part in many research projects financed by the European Union through Private-Public Partnership, including EFFRA and EGVI.
For videos of ESI’s Immersive Virtual Prototyping solutions, please visit ESI’s dedicated YouTube playlist.
Connect with ESI on LinkedIn, Twitter, Facebook, and YouTube
|
 |
December 1st, 2015 -
Enabling Die Engineering and Sheet Metal Forming from Concept to Production
ESI Group announces the latest version of its sheet metal forming simulation and die face design solution, PAM-STAMP 2015. Addressing the needs of OEMs and tier-suppliers in the automotive, aerospace and heavy industries, PAM-STAMP precisely predicts the outcome of complete sheet metal forming processes. For manufactures this means saved time and cost throughout the entire product development cycle — from conceptual design to try-out and production. For tooling suppliers, PAM-STAMP uniquely enables production die engineering by providing high quality, predictive simulation to support styling of outer panels and also the development of new lightweight structural parts.
" Car manufacturers aim to shorten their development cycles, sometimes to under a year. As a result, it is essential to forming operation and tool design engineers to be assured of very high surface quality early in the tool development cycle. " explains Harald Porzner, Director of Virtual Manufacturing Product Management at ESI Group. " Demand for accurate and defect free outer panels - especially with exciting stylings - has increased dramatically. Meeting that demand is even more challenging when using advanced material forming processes for structural parts. Reliable results in both cases depend on defining the tool geometry with great accuracy."
With these challenges in mind ESI delivers, with PAM-STAMP 2015, enhanced topology checking and geometry clean up and repair to enable most efficient geometry based die face design. Furthermore, with Die Starter, a brand new technology to generate the die surfaces needed to create a part, it is possible in the styling and design phase to generate fully automatically the die tools and to validate the forming results. The same technology can also be used in the concept development phase to generate automatically a starting point for refined die face design; saving a lot of iterations. By accurately accounting for all aspects of the stamping process PAM-STAMP enables full feasibility assessment early in the process. It supports tooling and design engineers from concept through selection of tooling methods to try-out and final production; predicting the outcome of every step in the manufacturing chain before making any real prototypes. PAM-STAMP’s results can be easily transported to ESI Virtual Performance Solution so that product performance models properly reflect the “as manufactured” components.
ESI PAM-STAMP comprehensively addresses splits, wrinkles, springback and cosmetic defects like shock and skid lines, ski lines, and sinks. Defects are a critical concern for both exterior parts and structural components; in one case negatively impacting the visual appearance, and hence the consumer’s perception of the product quality, and in the second case potentially compromising formability to the shape required to achieve light-weight and performance.
" Vesta uses PAM-STAMP constantly for several stamped parts and processes. Our main objective today is to prevent and solve aesthetical defects and to develop springback compensation strategies for various parts throughout the entire manufacturing cycle. " says Arlem Picinin Campos, Manager of Simulations and Machining at Vesta Engenharia, Brazil. With all the new developments it is now possible to manage cosmetic defects very early in the process and the structural performance at the right time, when designs are done.
With its particular capability to accurately simulate local bending and changing material properties, ESI PAM-STAMP 2015 provides even more accurate results. Developed over more than 25 years, in close collaboration with industrial and academic partners, PAM-STAMP addresses all types of sheet metal forming processes, including cold, warm and hot, and diverse metallic materials, including aluminum, titanium, and magnesium alloys, and different steels. Furthermore, the latest version of ESI PAM-STAMP adds a novel algorithm, based on an explicit computation strategy that delivers results three times faster than in the past. Coupled with the software’s capacity of directly using die surface designs from any CAD/CAE tool to simulation, engineers can realize time-savings of up to 90% as compared to traditional model set-up.
Accurate material information is crucial to successful simulations of sheet metal forming processes – which should be completed as early as possible in the development cycle. Addressing that issue, PAM-STAMP 2015 includes a new material database provided by an important partner of ESI; the Center of Precision Forming, at Ohio State University. In addition a new material law for hot forming (a unique strain path model) improves the precision of prediction of the geometry of the manufactured part; helping manufacturers better meet set tolerances. Heat generated as a consequence of friction work and plastic flow can now be included in the computation of the tool temperature when forming Advanced High Strength Steel (AHSS) and Ultra High Strength Steel (UHSS); providing superior simulation accuracy. Looking beyond the sheet metal forming process PAMSTAMP provides for advanced checking of the final part shape on the control table and an assembly module that has been added to enable checking of tolerances of assemblies with stamped components.
Notably, ESI PAM-STAMP 2015 includes enhanced capabilities and new modules for CAD cleanup, piece cost estimation, nesting (to minimize raw material waste) and die surface design. These modules work seamlessly with ESI’s platform Visual-Environment and Dassault Systèmes’ CATIA V5 to provide a very complete and efficient solution for sheet metal forming engineering.
" ESI’s new and enhanced PAM-STAMP solution excels in speed, capability, accuracy and efficiency, from design/styling to try-out. " concludes Harald Porzner.
Connect with ESI on LinkedIn, Twitter, Facebook, and YouTube |
 |
December 15, 2014 -
To leverage the use of Virtual Product Engineering For the Renewable Energies Market
ESI Group, pioneer and world-leading provider of Virtual Prototyping software and services for manufacturing industries, announces the signing of a strategic partnership agreement with EDF Energies Nouvelles (EDF EN). The partnership is in place for the next five years and will focus on innovative product development for the renewable energies market, leveraging ESI’s Virtual Prototyping technologies and expertise. New solutions and products co-created in the frame of this partnership will be exclusive to EDF EN.
Read more 
|
 |
December 15, 2014 - Recognition of the success of the international development of ESI Group
ESI Group, pioneer and world-leading solution provider in Virtual Prototyping, is announced the winner of the "Ambitions d’Entrepreneurs" Trophy in the "International" category.
Read more 
|
 |
December 15, 2014 -
ESI Group, pioneer and world-leading solution provider in Virtual Prototyping for manufacturing industries, announces the recent success of our client, SL Rasch: an architecture firm based in Germany that specializes in innovative buildings and lightweight structures. SL Rasch recently completed two complex architectural projects at the sacred sites of Medina and Mecca. The first was the design of foldable umbrellas that now protect pilgrims from the sun in the Medina Haram Piazza and the second was the design of the Mecca Royal Hotel Clock. Using ESI’s flagship software, Virtual Performance Solution, SL Rasch confidently investigated innovative designs and replaced physical models by virtual tests.
Read more 
|
 |
15 décembre 2014 -
-
Webinar 11 on December 19, 2014
Topic: Marine Modeling in VA One: a Highly Automated Vibro-Acoustic Simulation for the Marine Industry
-
Webinar 12 on January 9, 2015
Topic: Cabin Noise Simulation using VA One
-
Webinar 13 on January 16, 2015
Topic: Scripting Automation in VA One
-
Webinar 14 on January 23, 2015
Topic: Deterministic Simulation Methods for Vibro-Acoustics in VA One
-
Webinar 7 on January 30, 2015
Topic: Trim Modeling and Optimiziation

31 May 2015 – 5 Jun 2015 in Les Diablerets, Switzerland |
 |
January 7, 2014 -
ESI Group, pioneer and world-leading solution provider in Virtual Prototyping for manufacturing industries, announces the launch of a 6-year joint research program between Centrale Nantes and ESI, for which an Endowed Chair has been created. Both organizations will conduct advanced research on the topics of Model Reduction, Advanced Welding Simulation, and Thermoplastic Welding. The official inauguration will take place on January 21, 2014 at Centrale Nantes.
The research scope has been designed to solve current and future problems linked to advanced multi-material design and optimization strategies. “Centrale Nantes and ESI are joining forces to propose solutions that will raise the competitiveness of the French manufacturing industry and the country’s higher education alike,” says Dr Vincent Chaillou, COO, ESI Group.
ESI Group will be financing this 6-year collaborative research project, focusing on Model Reduction, Advanced Welding Simulation and Thermoplastic Welding.
Pr. Francisco Chinesta, Professor of Computational Mechanics at Centrale Nantes (France) and titular of the EADS Foundation Chair for the past four years, will be appointed “Centrale Nantes – ESI Chair”. Most specifically, he brings years of expertise in Model Reduction Strategies and advanced modeling and simulation of materials and processes. Dr Jean-Louis Duval, Platform Product Director, ESI Group, will oversee Model Reduction research operations on ESI’s side. Dr Yannick Vincent, Welding and Assembly Solution Product Manager, ESI Group, will coordinate the research on numerical simulation of welding processes, while Dr Laurent Dufort, Composites Manufacturing CoE Manager, ESI Group, and Dr Christophe Binetruy, from Centrale Nantes’ Materials, Processes and Composites department, will jointly lead the research on thermoplastics.
For Model Reduction Strategies, both organizations will work towards the development of virtual charts for non-linear models involving multiple parameters, by using the Proper Generalized Decomposition (PGD method). These virtual charts represent complex mathematical relationships at a glance, e.g. in the form of tables that can be easily visualized. They will be integrated in ESI software to deliver real time simulation results, optimization, and reverse analysis, with the aim to predict even faster how design and manufacturing changes (geometries, materials, processes) will affect a finished product’s performance.
For Advanced Welding Simulation, research will investigate Friction Steer Welding (FSW) processes, which enable the joining of dissimilar materials (such as steel and aluminum) in solid state. Another research objective will be to improve modeling techniques for additive manufacturing, as part of the welding process.
Today, out-of-autoclave systems based on thermoplastic materials are seen as a tangible solution to decrease process cost in the aeronautic and automotive industries. A research team will investigate this area, by focusing on the advanced simulation of automatic tape placement.
For students at Centrale Nantes, this initiative provides an opportunity to conduct teaching and research on topics that are directly in line with current and future industrial projects. It will finance four PhD theses around the above research projects, while the Research Institute of Civil Engineering and Mechanics of Centrale Nantes will strengthen its team with an additional research position in the field of Computational Mechanics.
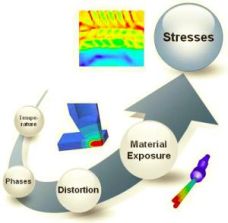 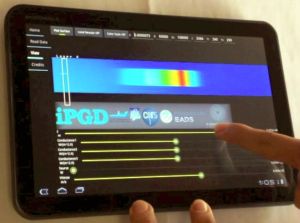
Challenges encountered during the numerical simulation of welding processes (left); and example of part of a virtual chart as used on a tablet (right)
|
 |
January 25, 2013 - |
Interview of Vincent CHAILLOU, ESI Group Product Operations President & CEO
ESI Group delivers Virtual Product Engineering solutions to various industrial sectors, combining 40 years of knowledge in the physics of materials with cutting-edge technology, and enabling its customers to create increasingly innovative products, faster and at a lower cost.
To this aim, ESI’s Virtual Prototyping software complements or even replaces physical prototypes, allowing its clients to control their manufacturing and assembly cycles step by step and in every detail, so as to anticipate any defect.
Customers including Astrium and Volkswagen Group use Virtual Manufacturing to predict the cause and effect relationships taking place in the fabrication of each component, sub-assembly and assembly to achieve a full end-to-end Virtual Prototype of their product – be it on the ground or in space.
ESI clients can then enter an optimization strategy, which involves increasingly larger models translating into larger size calculations! The rapid evolution of High Performance Computing is key to support the development of Virtual Performance Engineering. For example, using today’s powerful processing capabilities, ESI’s Composites Simulation Suite can now predict manufacturing defects for entire wind mill blades – something that would have been impossible with the technology that was available 5 years ago...
When the TERATEC campus was created, ESI immediately seized the opportunity to move in: joining other innovative companies in a team project environment would allow ESI to push the limits of known technology, drive ESI partners towards the adoption of its solutions, while benefiting from the latest technology designed to handle Big Data, and exploring the possibilities of Cloud Computing.
Today, ESI joins the Campus alongside partners such as Bull, Intel or the CEA, in an environment that promises to spur collaborative studies. |
|
Being present on the campus also allows ESI to strengthen its involvement in competitiveness clusters such as System X and Reg Innov, and places it conveniently close to the TGCC (Very Large Calculation Center). The creation of the Systematic lab has already helped Virtual Product Engineering progress. So has the Complex System Design Lab project, which was conducted in Cloud mode to allow for collaborative work, until its completion on September 30, 2013.
|
 |
About ESI group
is a pioneer and world-leading provider in Virtual Prototyping that takes into account the physics of materials. boasts a unique know-how in Virtual Product Engineering, based on an integrated suite of coherent, industry-oriented applications. Addressing manufacturing industries, Virtual Product Engineering aims to replace physical prototypes by realistically simulating a product’s behavior during testing, to fine-tune fabrication and assembly processes in accordance with desired product performance, and to evaluate the impact of product use under normal or accidental conditions. ’s solutions fit into a single collaborative and open environment for End-to-End Virtual Prototyping. These solutions are delivered using the latest technologies, including immersive Virtual Reality, to bring products to life in 3D; helping customers make the right decisions throughout product development. The company employs about 900 high-level specialists worldwide covering more than 30 countries. is listed in compartment C of NYSE Euronext Paris.
For more information about ESI, please visit:
Connect with ESI on , , and
ESI Group – Media Relations
Céline Gallerne
T: +33 (0)1 41 73 58 46
|
|
|